Um balanço dos trabalhos realizados
Escrito por Ana Cardoso
Fotografias de Luís Viegas
O shutdown de inverno foi marcado por um esforço intenso de modernização e manutenção nas instalações. Com 98% dos trabalhos planeados concluídos, o avanço nas melhorias de infraestrutura e processos reafirma o compromisso da empresa com a excelência operacional e a segurança. Ao todo, foram executados 160 projetos, dos quais 20 foram considerados relevantes para o inicío de produção do novo carro e concluídos integralmente.
Foram realizados 24 projetos nas Prensas, 30 nas Carroçarias, 21 na Pintura, 45 na Montagem, 20 nas Infraestruturas e 3 na Logística, além de 2 projetos na Unidade de Negócios de Cunhos e Cortantes.
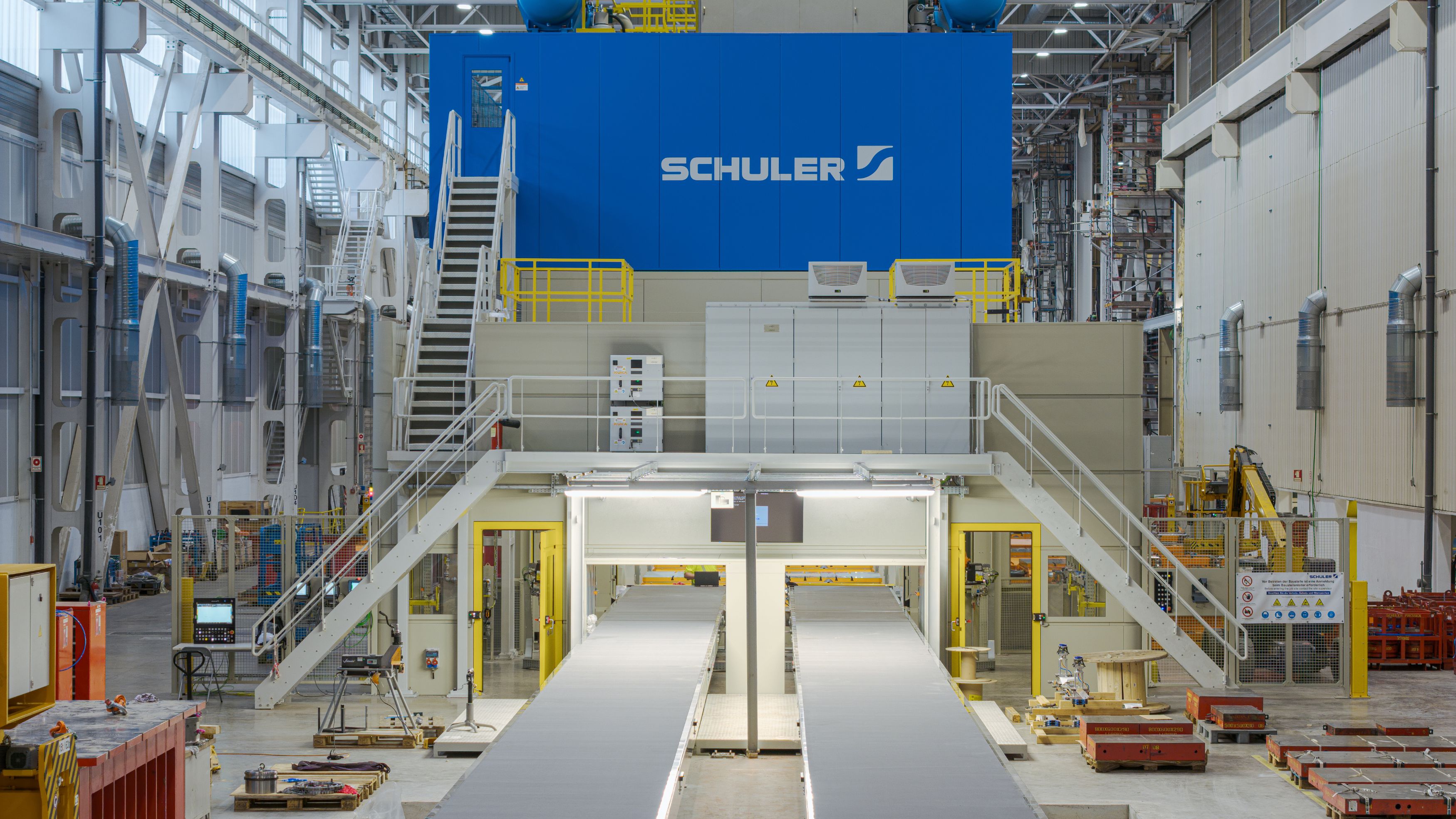
-
Modernização no shutdown | Um balanço dos trabalhos realizados
Prensas
-
Entre os projetos mais significativos, destaca-se a instalação da nova PXL, que será crucial para a produção do novo modelo. A PXL não só permitirá aumentar a capacidade produtiva, como também trará melhorias substanciais em termos de eficiência e qualidade na estampagem das peças.
-
Entre os projetos mais significativos, destaca-se a instalação da nova PXL, que será crucial para a produção do novo modelo. A PXL não só permitirá aumentar a capacidade produtiva, como também trará melhorias substanciais em termos de eficiência e qualidade na estampagem das peças.
-
Durante a paragem da nossa fábrica e das demais fábricas para as quais exportamos as peças que produzimos na área de Prensas, aproveitou-se a disponibilidade das prensas para trabalhos de melhoramento e produção antecipada de peças de pré-série. Destaca-se a integração das ferramentas das portas interiores do projeto do novo carro, levada a cabo pelos colaboradores da Unidade de Negócios de Cunhos e Cortantes. Também foram antecipadas o maior número possível de produções de outras peças do mesmo projeto, evitando assim afetar mais tarde o normal desenvolvimento da produção na área.
-
Durante a paragem da nossa fábrica e das demais fábricas para as quais exportamos as peças que produzimos na área de Prensas, aproveitou-se a disponibilidade das prensas para trabalhos de melhoramento e produção antecipada de peças de pré-série. Destaca-se a integração das ferramentas das portas interiores do projeto do novo carro, levada a cabo pelos colaboradores da Unidade de Negócios de Cunhos e Cortantes. Também foram antecipadas o maior número possível de produções de outras peças do mesmo projeto, evitando assim afetar mais tarde o normal desenvolvimento da produção na área.
Montagem
Foram instaladas calhas gravíticas para otimizar o retorno dos MFTs (Multi-Function Tester - equipamentos utilizados em testes elétricos), com cerca de 3,5 kg. Na zona B, o número de estações de testes elétricos aumentou de 3 para 6, exigindo a realocação para a plataforma. Na zona E, as estações passaram de 3 para 5,5, com duas calhas gravíticas instaladas para garantir maior eficiência. Na zona J, a calha do lado direito foi realocada para o esquerdo, eliminando a curva em "Z" e reduzindo o retorno dos MFTs para 76 metros em menos de 1 minuto. A segurança foi uma prioridade em todas as implementações, por isso, foi instalada uma tranca dupla em todas as calhas, que reforça a estabilidade e minimiza os riscos associados ao manuseamento dos equipamentos durante o processo de retorno.
Foram instaladas calhas gravíticas para otimizar o retorno dos MFTs (Multi-Function Tester - equipamentos utilizados em testes elétricos), com cerca de 3,5 kg. Na zona B, o número de estações de testes elétricos aumentou de 3 para 6, exigindo a realocação para a plataforma. Na zona E, as estações passaram de 3 para 5,5, com duas calhas gravíticas instaladas para garantir maior eficiência. Na zona J, a calha do lado direito foi realocada para o esquerdo, eliminando a curva em "Z" e reduzindo o retorno dos MFTs para 76 metros em menos de 1 minuto. A segurança foi uma prioridade em todas as implementações, por isso, foi instalada uma tranca dupla em todas as calhas, que reforça a estabilidade e minimiza os riscos associados ao manuseamento dos equipamentos durante o processo de retorno.
A realocação dos processos e equipamentos da zona B para a zona E foi motivada pela necessidade do novo carro precisar de mais estações para os testes elétricos. Esta alteração permitiu duplicar o número de estações de testes elétricos atuais (de 3 para 6 estações) e, por conseguinte, ter mais módulos comissionados. Teve também um impacto positivo nos testes elétricos do modelo atual, pois conseguimos ter mais estações para eventuais reparações.
A nova geração de manipuladores gravidade zero, feitos de carbono e totalmente pneumáticos, são projetados para auxiliar na montagem de peças novas e pesadas do novo carro na Volkswagen Autoeuropa. Adaptados às necessidades específicas, permitem aos operadores manusear cargas como uma extensão do braço humano, garantindo ergonomia, segurança e precisão. São ideais para movimentos rápidos e repetitivos e também reduzem esforços físicos e riscos de acidentes de trabalho.
Para a integração do novo modelo no Engine Line, foram necessárias modificações nos quadros de montagem nas linhas de submontagem do Engine Dress e Powertrain, bem como novos quadros no Powertrain. Também novas automações tiveram de ser construídas de raíz, para produzir a variante híbrida do novo modelo. Assim, foi criada uma nova linha de submontagem das baterias e para montagem, transporte e manuseio da bateria, foram adotados veículos autónomos. Para transferência entre linhas de montagem foi instalada uma automação com dois robôs. Já para o aperto do suporte de apoio do motor, foi criada uma nova automação na linha do Decking, com um robô aparafusador alimentado automaticamente. A adição das novas instruções de montagem nos ecrãs computorizados de cada estação, bem como a sua interligação com os scanners dos componentes de segurança e o desbloqueio das ferramentas de aperto e a comunicação dos seus torques para registo e rastreabilidade do produto, tiveram de ser garantidas. De modo geral, os computadores de controlo das linhas de submontagem sofreram uma intervenção de modo a aceitar o novo modelo e as suas variantes.
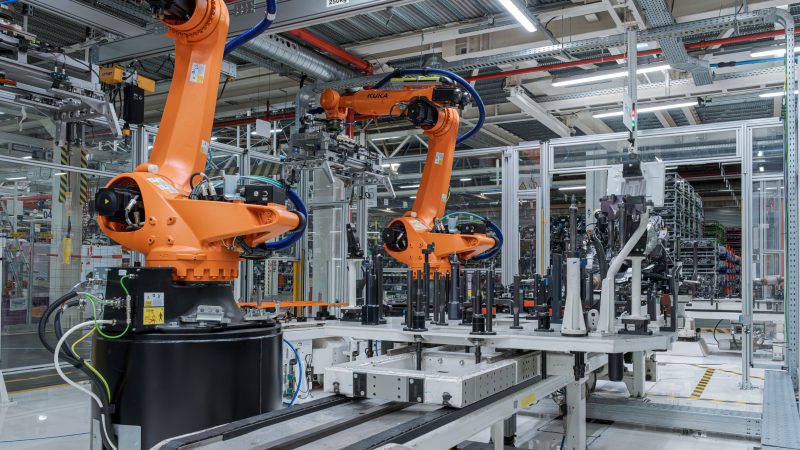
Além dos projetos específicos, também foram realizadas importantes ações transversais, como a desinfestação completa dos balneários, reparações nos pisos de todas as áreas, melhorias no sistema de água potável, trabalhos de manutenção na água de resfriamento na PXL, manutenção no barramento elétrico e no sistema de extração de cozinhas, além de ajustes nos robôs e no armazenamento do NPM.
A segurança foi uma prioridade durante os trabalhos, o que se reflete na contabilização de 8 acidentes e 3 incidentes.
O sucesso do shutdown foi possível graças ao esforço conjunto de uma média diária de 321 colaboradores internos da Volkswagen Autoeuropa e 534 profissionais externos.
Social Media