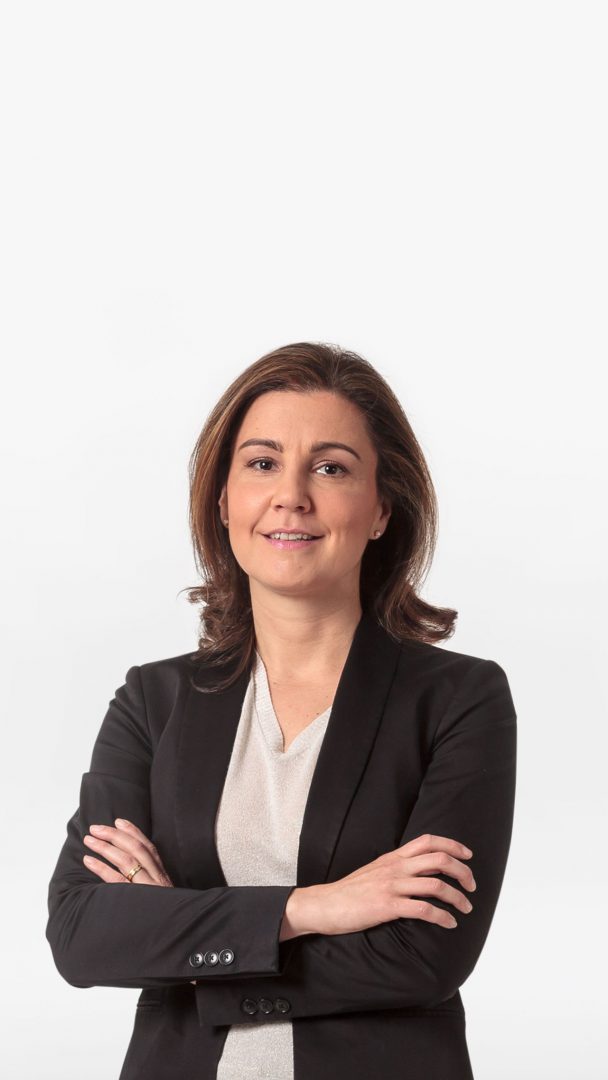
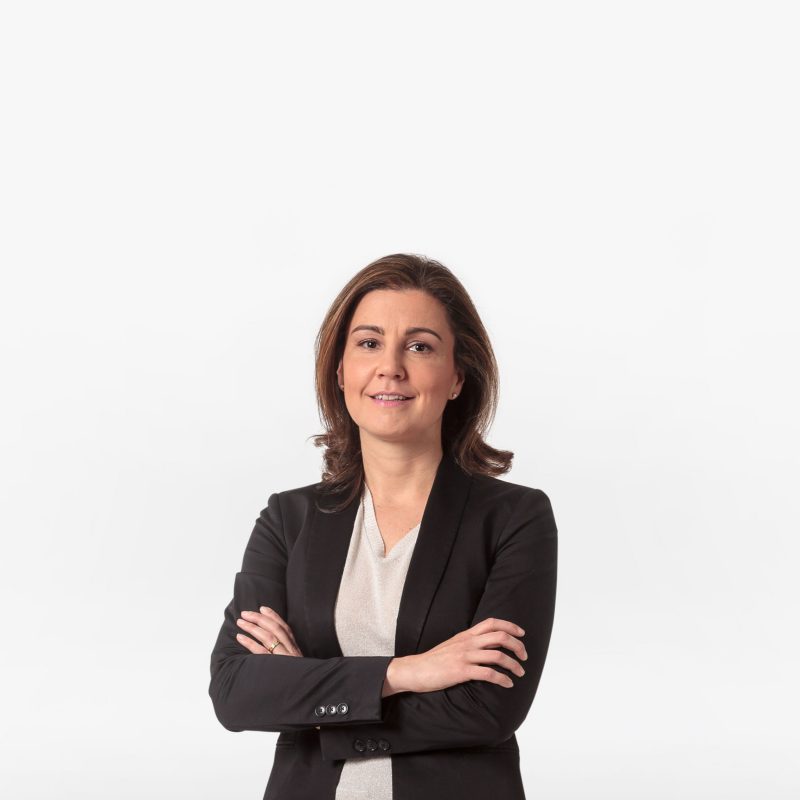
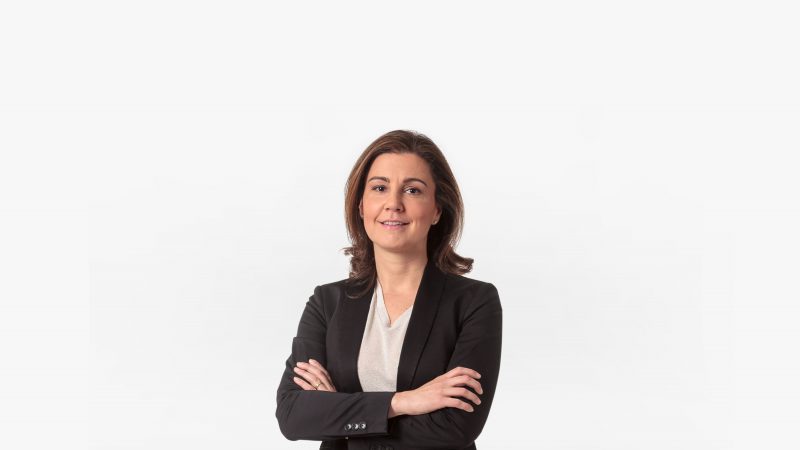
Produce.Together
Fábricas sustentáveis e de baixo custo
- 1
-
Margarida Pereira, mentora do campo de ação e diretora da área de Gestão de Produto e Planeamento
Para o topo da página
-
Fábricas sustentáveis e de baixo custo
Apresentamos o sexto campo de ação do Produce.Together: Fábricas sustentáveis e de baixo custo e os seus principais projetos para 2021.
O propósito deste campo de ação é reduzir os custos de fábrica e evitar investimentos através da partilha de boas práticas, estabelecendo sinergias globais entre as várias fábricas do Grupo Volkswagen. Como? Através da concretização de projetos de transformação e de otimização que, tendo por base a introdução de novas tecnologias e de novos processos, visam impulsionar a sustentabilidade das fábricas.
Durante o ano de 2021, houve um investimento total de 820 mil euros nas medidas já implementadas deste campo de ação. As poupanças ascendem a quase 1 milhão e 200 mil euros.
Em todas as medidas, e em particular no bicolor da Pintura, destaca-se a inovação simples e focada no utilizador, através do envolvimento intenso dos colaboradores, traduzindo-se em benefícios ergonómicos, redução de desperdício, melhoria de qualidade/ redução de retrabalho, entre outros.
Automação da pré-montagem do eixo traseiro
Na Montagem, mais concretamente na estação PA80, foi instalado um robô que recolhe o eixo traseiro de acordo com a sequência logística no rack e coloca-o na plataforma de pré-montagem do chassis do carro.
«Resolvemos, assim, os problemas de qualidade causados por danos devido a eventuais colisões durante o posicionamento manual assistido com guincho do eixo na frame de pré-montagem. As colisões advêm da elevada inércia angular dos eixos.
Com efeito, as reduzidas tolerâncias no posicionamento dos eixos por entre a concentração de pinos da frame de pré-montagem não são compatíveis com uma operação manual, ainda que assistida por um guincho.», explica Luís Oliveira, especialista de planeamento da Montagem, GPP.
O arranque ocorreu no passado dia 24 de setembro: «Neste momento estamos a proceder aos ajustes finos da automação e dos elementos que dela fazem parte, como por exemplo as frames e o sistema de visão artificial, que podem de certa forma ser considerados os componentes críticos nesta automação. O sistema foi desenvolvido internamente, aproveitando o conhecimento e a experiência da nossa Manutenção.», comenta Oliveira.
Este investimento de 300 mil euros trouxe vários benefícios, refere João Batata, coordenador de turno do Finish da área da Montagem: «Este projeto foi inteiramente desenvolvido in-house. Demonstra, mais uma vez, a enorme capacidade que temos em implementar ideias que visam sempre a otimização de processos e operações. Acima de tudo, mostra a nossa enorme capacidade de reaproveitamento de materiais e equipamentos, que de outra forma seriam obsoletos, como é o caso do robô ali instalado. Com este projeto conseguimos ainda melhorar as condições ergonómicas da estação e o indicador de produtividade da fábrica.»
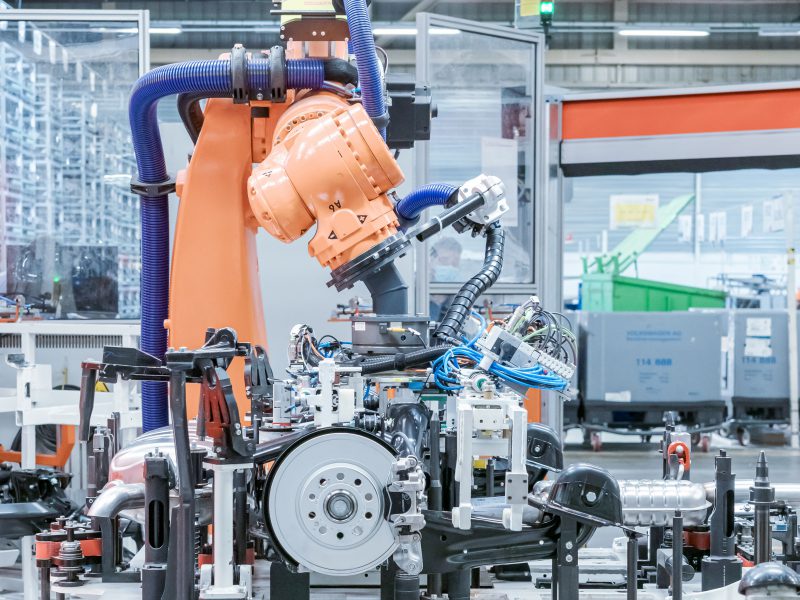
Aplicação automática de fita no portão traseiro
No processo de pintura do bicolor, é necessário isolar a pintura do tejadilho por trás do portão traseiro (tailgate). Atualmente dois MRK, robôs colaborativos, realizam a aplicação automática da fita de mascaramento.
Este processo automático está em funcionamento desde maio e tem estado a receber melhorias no sentido de aumentar o uptime.
Anteriormente, o processo era todo manual, usando uma fita dupla bastante dispendiosa. Além da aplicação ter sido automatizada, foi construída uma máquina dispensadora de fita que utiliza material mais barato do que o processo original. Todo o desenvolvimento e implementação foi da responsabilidade da equipa de MPs do bicolor, tendo sido os robôs adquiridos a um fornecedor.
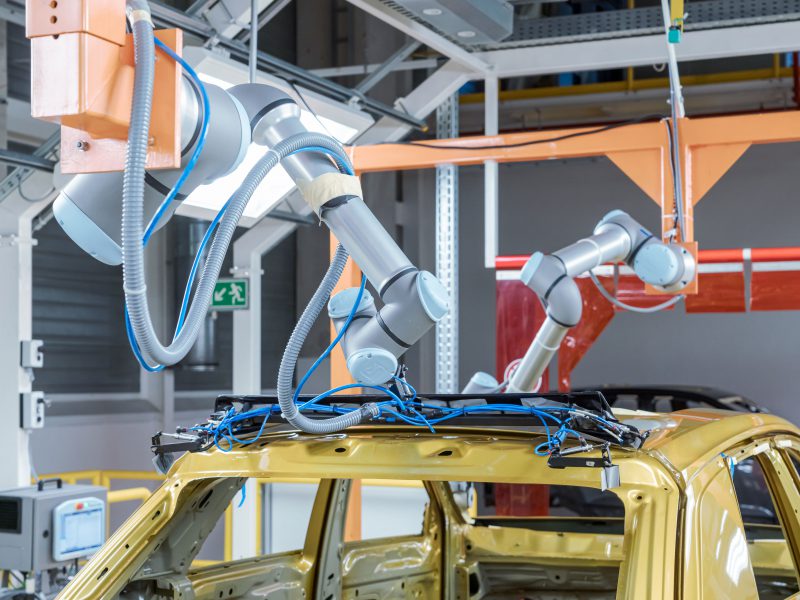
Plataformas móveis nas linhas da Pintura
A instalação das quatro plataformas nas zonas de inspeção da Pintura e no Finish da Montagem tem como objetivo agilizar a passagem dos operadores de produção de um lado para o outro da linha, para que o mesmo operador consiga executar tarefas tanto no lado direito, como no lado esquerdo do carro. «Temos um aumento de versatilidade e redução de desperdício nas deslocações dos operadores. Adicionalmente ainda conseguimos uma melhoria da condição ergonómica da estação sem comprometer o tempo de ciclo de produção.», explica Sérgio Marques, especialista de planeamento na área de GPP e responsável pela coordenação e instalação dos novos equipamentos de plataformas móveis em várias zonas na área da Pintura. Estas novas estruturas estão operacionais desde o final do shutdown de verão e, atualmente, estão em fase de otimização.
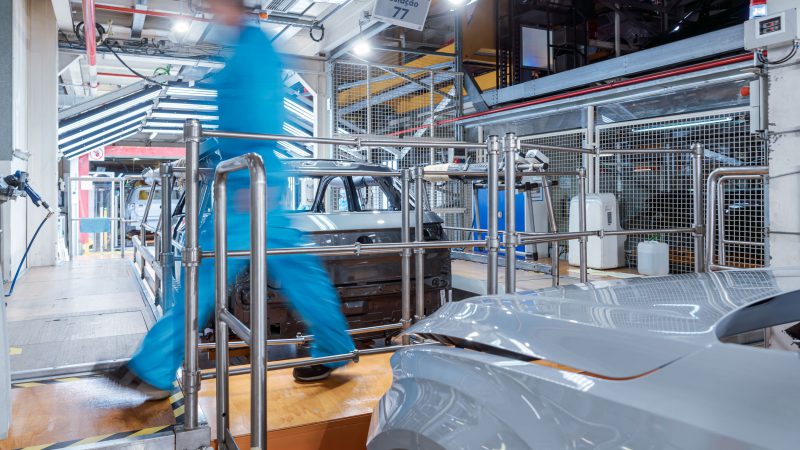
Social Media